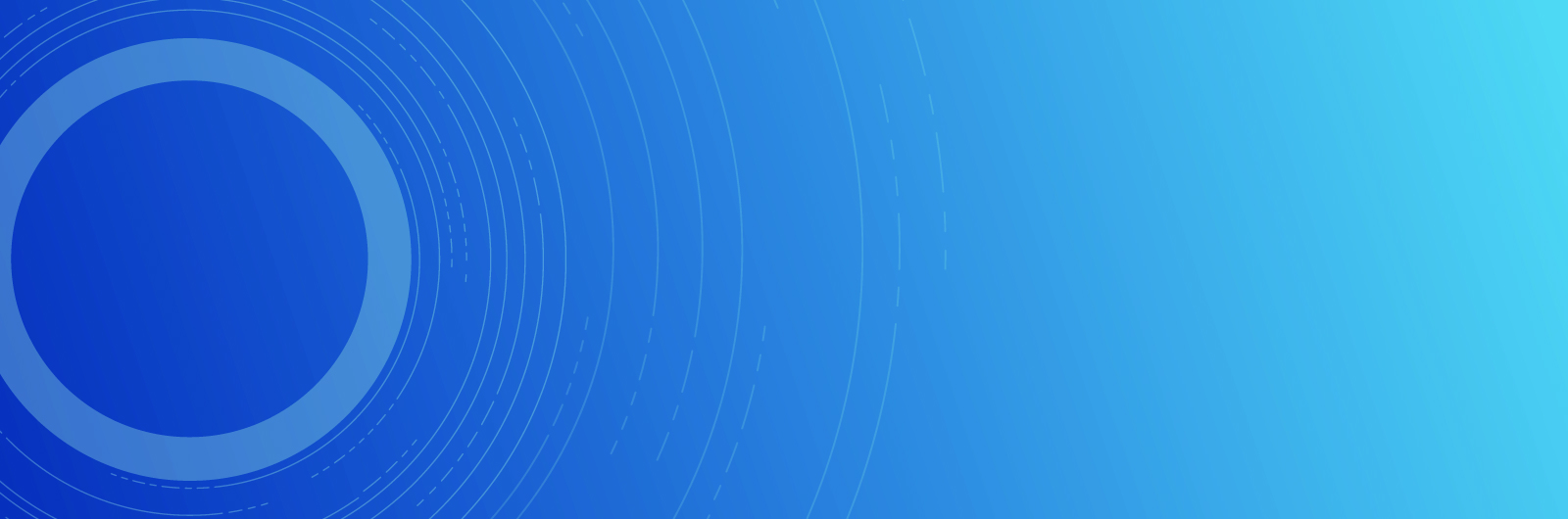
Polyethylene capacity continues to grow with China leading in number and volume additions
Polyethylene capacity continues to grow with China leading in number and volume additions
World polyethylene capacity continues to grow with large-scale plant investments being made globally through the next 10 years. Most impressive will be China’s growth, both in number of plants and volume amount, despite US feedstock advantages. China continues to strive toward self-sufficiency into 2024 (already at 68% in 2023), much like China’s recent success in polypropylene.
Already carrying nearly one-third of the world’s total PE capacity, China’s capacity will continue to grow with most new additions in LLDPE followed by HDPE and then LDPE. Based on current announcements, additions will ramp up through 2028, similar to the expansion seen between 2019-2022. Most of the new capacities are integrated based on naphtha, which maintains competitiveness in terms of capital expenditure and operational costs.
Of continued interest is the increase of LDPE capacity in China, with the addition of 1170kt in the next four years, while North America and Western Europe have no anticipated capacity in the same time span. These smaller capacity autoclave plants are ideal for making EVAs (a LDPE derivative) commonly used in solar panels and shoe soles (China is the world’s largest shoe producer). These investments in LDPE/EVA further support China’s ambitions to be a world leader in solar panels and the energy transition.
Comprehensive world growth, including China, is not without growing pains as producers will need to consider how to manage timing of new capacity additions alongside inflation and macro-economic conditions. Producers will have to monitor a delicate situation of not exacerbating supply pressure both locally and globally, especially in China as the rate of oncoming capacity will reduce imports and impact regions such as the SEA and the USA. Globally, the long-term growth outlook for polyethylene is promising, particularly in Northeast Asia.
The data and insight used in this article comes from the new Argus Polyethylene Analytics service. Request more information here.
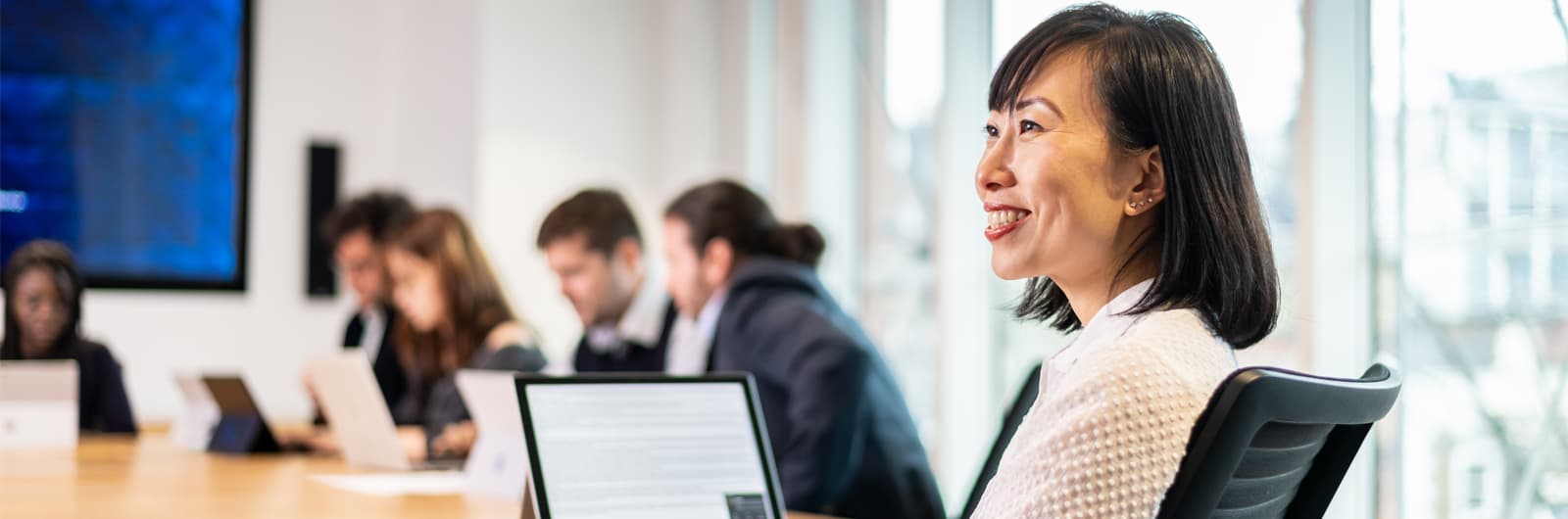