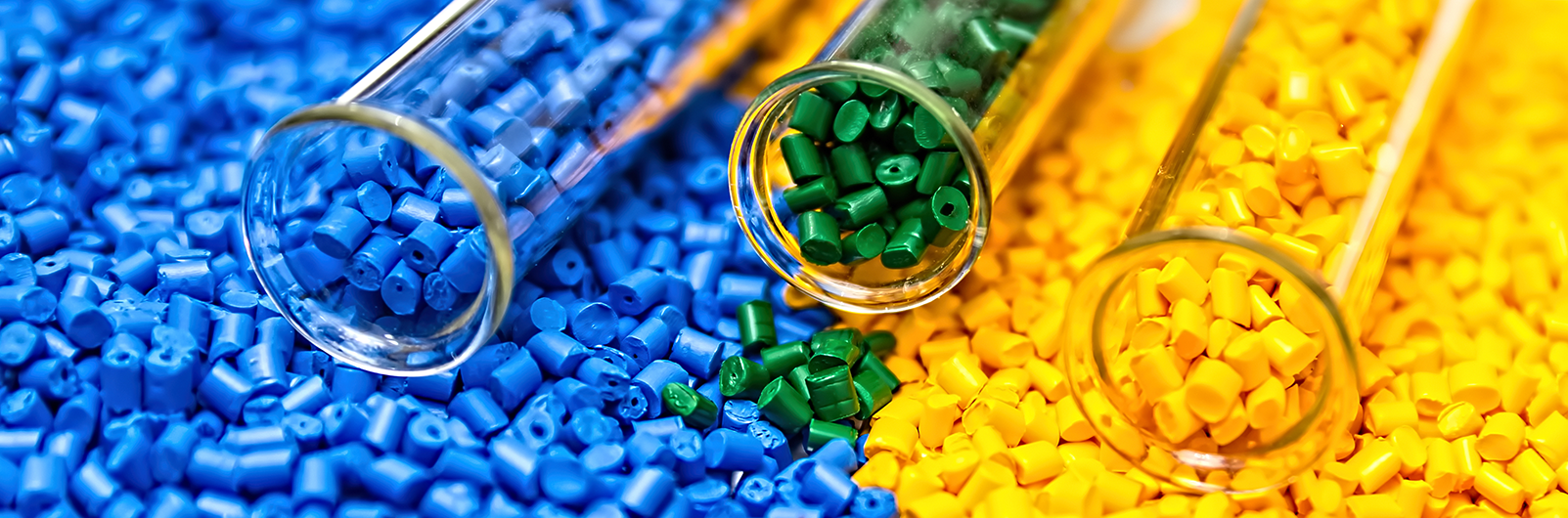
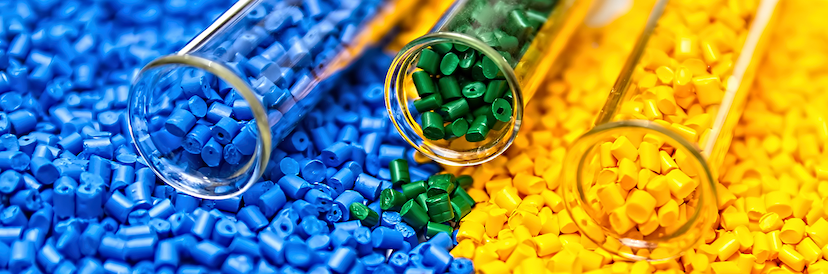
Polymers
Overview
Global polyethylene (PE) and polypropylene (PP) supply and demand dynamics are in transition. Supply is increasing much faster than demand and international trade is shifting due to political and economic events. About 40% of the US polyethylene production is exported, mainly to Asian markets, whereas only about 10% of the polypropylene production is exported, mainly to LATAM markets.
Ethylene prices in Asia and Europe are tied to naphtha whereas ethylene prices in the US are impacted by natural gas and ethane supply. Asia is also self-sufficient on PP whereas they must import 25% of their PE demand.
The impacts of other ethylene and propylene derivatives such as PVC or propylene oxide also require assessment.
Our polymer experts will help you determine what trends to track and how to stay competitive in today’s ever-changing global markets.
Latest polymers news
Browse the latest market moving news on the global polymers industry.
Lummus, MOL to build Hungary pyrolysis plant
Lummus, MOL to build Hungary pyrolysis plant
London, 11 July (Argus) — Technology licenser Lummus and Hungarian oil firm Mol have started construction designs for a pyrolysis chemical recycling plant at Mol's site in Tiszaujvaro, Hungary. It will have a processing capacity of 40,000 t/yr of mixed plastic waste. The plant will produce pyrolysis oil for the Mol petrochemicals facility at the same location, which has a capacity of 660,000 t/yr for ethylene and 335,000 t/yr for polymer-grade propylene. Mol and Lummus signed an agreement to integrate pyrolysis chemical recycling at its refining and petrochemical sites in Slovakia and Hungary in 2023 . Mol indicated at the time it aimed for production capacities of more than 100,000 t/yr of recycled plastic by 2030. By George Barsted Send comments and request more information at feedback@argusmedia.com Copyright © 2024. Argus Media group . All rights reserved.
Borealis to keep pyrolysis options open
Borealis to keep pyrolysis options open
London, 28 June (Argus) — Austrian chemical company Borealis continues to weigh up the technology pathways for expanding pyrolysis chemical recycling capacity. A plan to build a plant in Stenungsund, Sweden, was put on hold earlier this year, and the company might opt for a different location altogether. The Stenungsund project has yet to get past the feasibility stage as it had "not yet met the performance requirements expected". The company said earlier this year that it was evaluating different technology options for the site, including the Blue Alp pyrolysis process in use at its majority-owned Renasci plant in Ostende, Belgium, and parent company OMV's ReOil technology, which is to be deployed at small commercial scale in Schwechat, Austria, this year. Borealis vice-president of circular economy Mirjam Mayer told Argus at PRSE that the chemical recycling investment environment has become more challenging: "A lot of projects across the industry have been delayed... with capital expenditure increases seen recently." But she said Borealis remained committed to adding chemical recycling capacity and was looking at investment options. These could include new technologies or different locations, Mayer said, noting that there was "greater flexibility for chemical recycling scope in the Nordic area". Stenungsund was initially due to start up this year, providing recycled feedstock to count towards Borealis' target of producing 600,000 t/yr of recycled and bio-based polymers by 2025. Mayer said the company is still committed to its goal, but acknowledged it could be challenging in current market conditions. In the last few years Borealis has acquired both chemical and mechanical recyclers and Mayer said Borealis was "still open to mergers and acquisition opportunities, as long as they made sense, but a starting point going forward would be to expand on opportunities from recently bought companies, including Rialti, Renasci and Integra Plastics". "We have made some good progress, especially with acquisitions in the last year or so, and there seems to have been a real step change in the last year... with current capacity of around 200,000 t/yr [for these products]," Mayer added. Rising costs, including new projects' capital expenditure requirements and energy prices, have checked progress in recent years, Mayer said, as has competition from cheap virgin material. Meyer also said EU Packaging and Packaging Waste (PPWR) regulations have bought "clarity and security" to the industry for 2030, but that volatile energy costs might contribute to weak market conditions in the short term. "Regulatory support, like PPWR is something we need to make progress and make these targets a reality," she said. Some companies have announced closures or strategic reviews of European petrochemical assets in recent months, highlighting the challenge facing the industry, but Mayer said Borealis feels it is in a better position in Europe as it covers "a specialty segment which is valued by customers and sells products that actively support the energy transition". This includes its focus on building a portfolio of sustainable products, including its Borcycle-M mechanically recycled polymer range and Borcycle-C chemically-recycled product line, she said. Borealis recently achieved US Food and Drug Administration approval for some Borcycle-M grades, which Mayer called a "very important step" in being able to take recyclates to a wide variety of consumer applications, including cosmetic, personal care and dry food packaging applications. Send comments and request more information at feedback@argusmedia.com Copyright © 2024. Argus Media group . All rights reserved.
PRSE: Brighter notes, familiar chords
PRSE: Brighter notes, familiar chords
London, 28 June (Argus) — In our editorial following last year's PRSE trade fair, we discussed short-term concerns and long-term optimism for the industry. This year's show — held last week in Amsterdam — featured some brighter notes, but conversations also struck many familiar chords of pessimism about the near term. On the plus side, last year's main reason for long-term optimism — increasingly supportive legislation in Europe — remains on track. The EU Packaging and Packaging Waste Regulations (PPWR) mandating recycled content across almost all plastic packaging by the end of the decade appear set for confirmation in the near future — welcome news for polyolefin recyclers in particular. And the PE films market appears less nervous about PPWR's strict reuse quotas for industrial packaging than it was in spring, with much optimism that future delegated acts will address industry concerns. Importantly for chemical recyclers, the European Commission has continued to support fuel use-exempt mass balance accounting, with member states reportedly largely in line. For PET recyclers, mandatory recycled content requirements are even closer, with the 25pc minimum for PET beverage bottles kicking in from next year. The weather has not generally supported a strong season for on-the-go beverage consumption in much of Europe this year, limiting the emergence of a peak season for rPET pellet consumption. And there is a feeling that the supply chain is more adequately stocked ahead of next year than it otherwise would have been, even as a reduction in the competitiveness of imports from Asia — the result of higher freight costs — theoretically supports demand for European recyclates. But PET recyclers were quietly confident about future demand prospects because of the upcoming regulation. Demand for premium blow-moulding grade rHDPE was another bright spot discussed at the fair, with many recyclers operating in that market noting increasing buying interest. This is an encouraging sign, one said, that brand owners are still looking to make as much progress as possible towards their 2025 targets for recycled content in packaging, after a slowdown in new projects last year, despite recent data showing that many are not on track to fully meet them. But for all the upbeat sentiment, many of the same concerns were raised again at this year's gathering. Polyolefin recyclers complained of low or even negative margins on commodity cost-saving products, such as low-end rPP grades and rHDPE pipe, with virgin PE and PP prices having declined in recent months and underlying demand still slow. There was still a feeling that a challenging period lies ahead, and that this could lead to further consolidation in the industry. And progress towards EU legislation supporting demand for recyclates outside of the packaging industry has been comparatively slow since the previous PRSE — save for a proposal from the commission to mandate 25pc recycled content in automotive plastics. Aside from concerns about sales volumes and margins, challenges with feedstock sourcing have come tgo the fore again in 2024, particularly in the flexible PE market. Flexible PE bale prices have risen through the second quarter because of reduced production of waste from commercial sites and, more recently, strong demand for exports to southeast Asia. Recyclers have struggled to pass on increases to their pellet customers, resulting in a squeeze on their margins. Since the last PRSE, the confirmation of EU waste shipment regulations (WSR), which will ban plastic waste exports to non-OECD countries from November 2026, will reassure recyclers concerned about feedstock supply. WSR might turn out to have a similar or even greater impact on the flexible PE recycling market than the more-publicised PPWR. The 27 EU countries exported 33,000 t/month of flexible PE waste to non-OECD countries — mainly in southeast Asia — in the first four months of this year, according to data from Global Trade Tracker. This is equivalent to 15-20pc of the volume of post-consumer PE film waste that is recycled in Europe, according to the latest Plastic Recyclers Europe data. Keeping this material in the European market would naturally be expected to increase feedstock availability for European recyclers. But it would be an oversimplification to say that cheaper input costs for recyclers will be the only result. European capacity will also need to adapt to accepting more export-quality bales, which are typically seen as lower-specification 98/2 or less transparent fractions. And demand for feedstock in Europe is also likely to increase, including through companies currently involved in exporting bales — many of which are already recyclers or affiliates of recyclers — that are building or expanding European recycling capacity. It was clear at the last PRSE that the myriad challenges facing the European recycling industry were not going to have evaporated by the time this year's show came around. The mood overall felt more positive than last year, but the hatches remain battened for many recyclers, with a challenging few months or even years still expected ahead. EU-27 LDPE waste exports Send comments and request more information at feedback@argusmedia.com Copyright © 2024. Argus Media group . All rights reserved.
Dow to buy flexible plastics recycler Circulus
Dow to buy flexible plastics recycler Circulus
Houston, 25 June (Argus) — US-based chemical producer Dow has agreed to acquire Oklahoma-based flexible plastics recycler Circulus, part of Dow's efforts to expand its recycled polymer offerings. Circulus has mechanical recycling facilities in Ardmore, Oklahoma, and Arab, Alabama, with a combined input capacity of 50,000 metric tons/yr (110mn lb/yr) of flexible polyethylene. The deal is expected to close in the third quarter, Dow said. Financial details were not disclosed. The acquisition marks Dow's first purchase of a recycling facility as the company seeks to produce 3mn t/yr of circular and renewable plastic by 2030. Dow said the purchase of Circulus will help enhance its offerings in applications such as shrink packaging, stretch film, and food packaging. Dow has previously been active in recycled polymers markets, partnering with WM in 2022 to collect residential film in a pilot program , and partnering with Closed Loop Partners to create a circular plastics fund . By Zach Kluver Send comments and request more information at feedback@argusmedia.com Copyright © 2024. Argus Media group . All rights reserved.
Spotlight content
Browse the latest thought leadership produced by our global team of experts.
Explore our polymers products
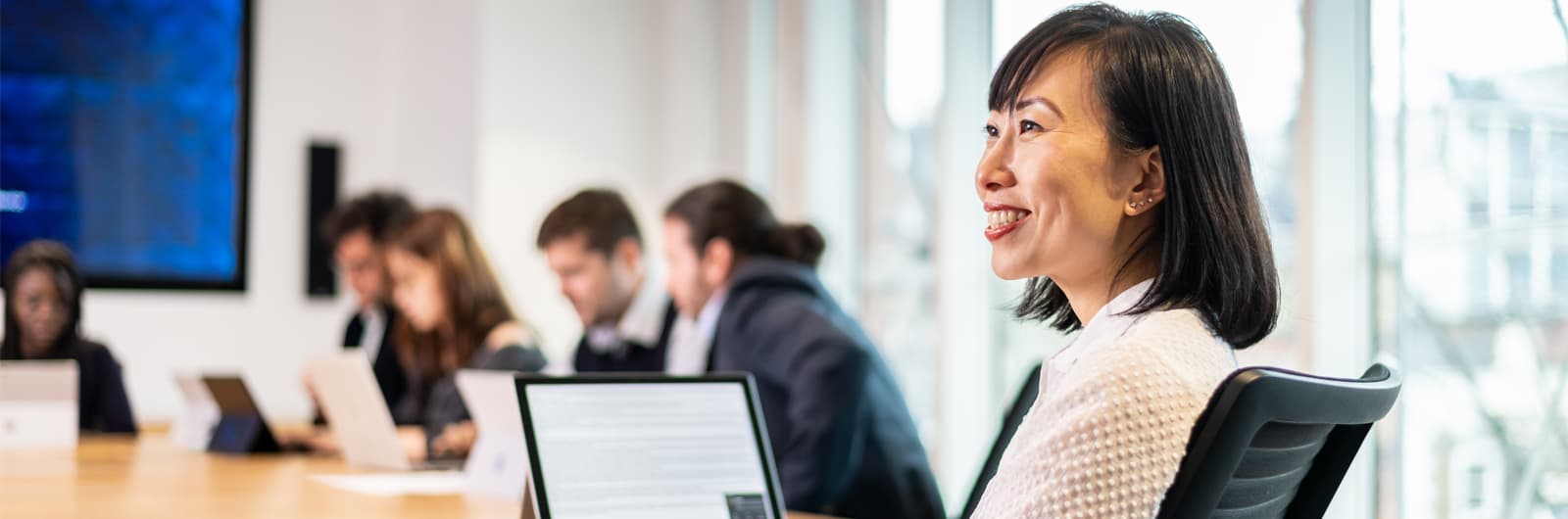