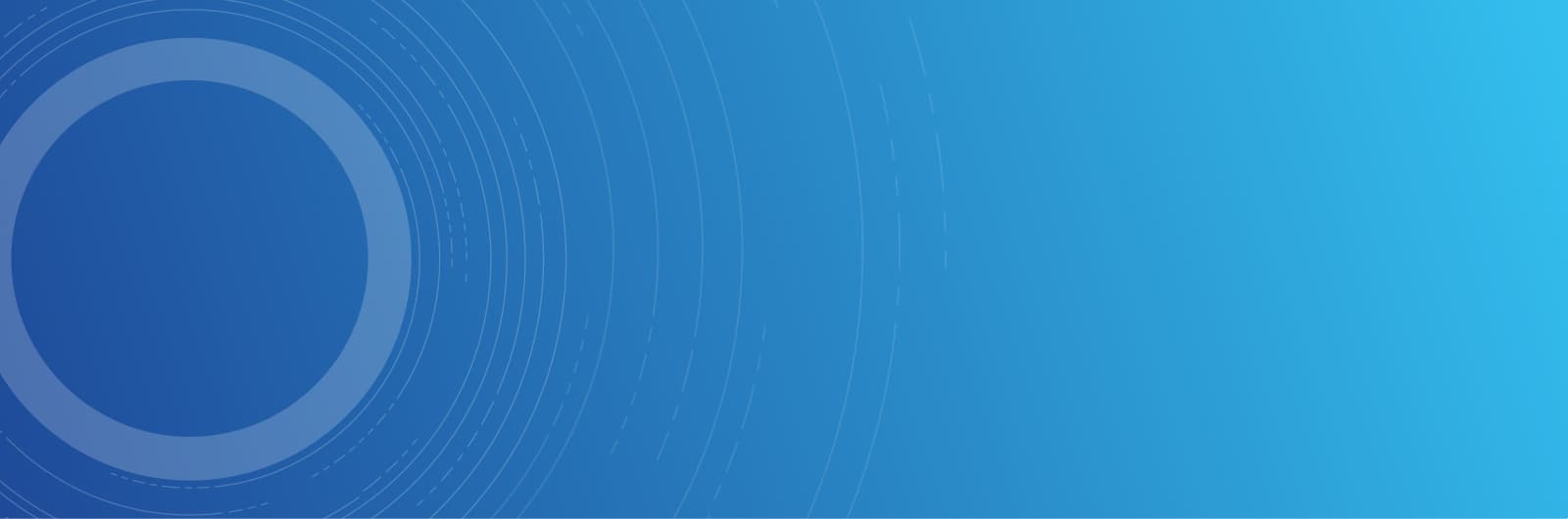
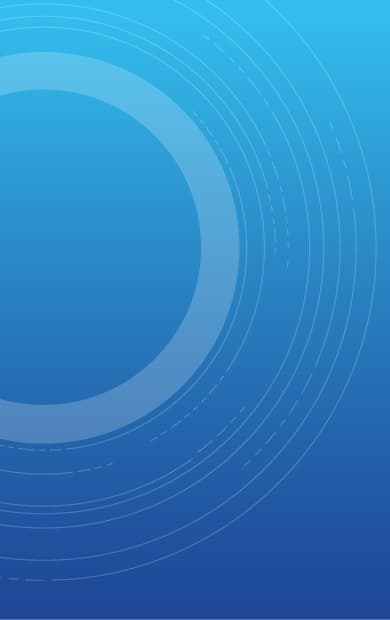
Market opinion and analysis blog
Overview
Through the Argus blog, our team of 600+ commodity market experts provide opinions and analysis on the key themes and topics shaping energy and commodity markets around the world. These insightful articles are relevant and timely view points to help you better understand the constantly changing landscape of the markets that matter most to you.
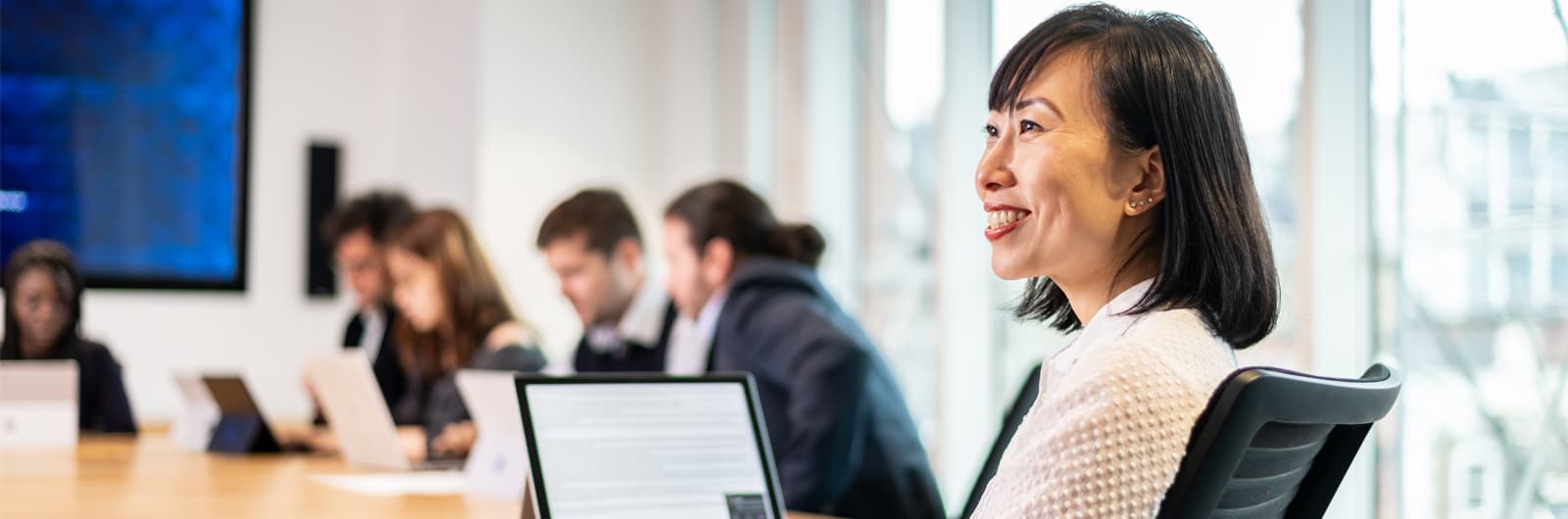
Speak to our experts today:
Register below and we will customize a solution that meets your exact needs. When you speak to one of our experts, you may be qualified to sample our industry-leading products on a no-cost basis.
You can unsubscribe from these updates at any time. We manage your personal data in accordance with our privacy policy.