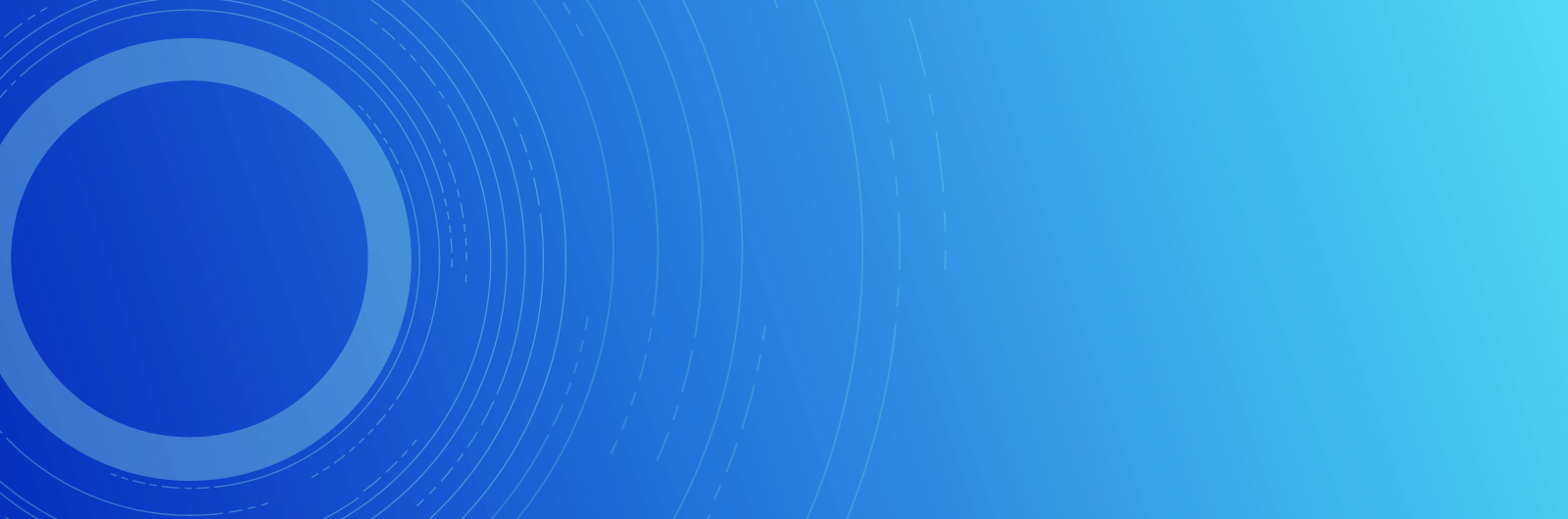
Single-family housing construction up, but overall housing market weakness is blow to construction-facing polymers
Single-family construction permits and starts both rose in September, but weakness in the broader housing market continues to pressure PVC and Polyurethane as the year comes to a close.
Single-family permits rose to a seasonally adjusted annual rate of 965,000 in September, 1.8pc higher than August and 11.6pc higher year-on-year, according to the US Census Bureau and the Department of Housing and Urban Development (HUD). It continues the month-to-month growth in single-family permits that has lasted since the start of the year.
Single-family starts rose to the third highest level of 2023 with a rate of 963,000 units, 3.2pc higher than August and 8.6pc higher year on year. The growth in the single-family construction sector has helped make the latter half of the peak building season stronger for PVC compared to the first half of the season.
PVC buyers and converters have claimed better demand in August and September compared to the early summer, with October being steady or even slightly better still. Domestic contract prices for PVC have largely held flat during this time, rising 2¢/lb in August to 59.5¢/lb before rolling over in September with October potentially doing the same.
Prices for isocyanates such as methylene diphenyl diisocyanate (MDI) have been flat for the last few months after steady decreases through 2023. Prices for polyether polyols have followed a similar trend, stabilizing in the last few months after a previously consistent downward trend.
Broader market
Even as some positive signs persist in the single-family construction sector, broader homebuilding dynamics present more of a mixed picture that has presented limitations on demand growth for construction polymers. September’s rate of 1.358mn housing starts was 7pc above August, but still 7.2pc lower than September 2022.
The divergence of trends between single-family construction and the broader market weakness is owed to multi-family homebuilding. Starts for units of five or more, namely apartment complexes, was at a rate of 383,000 in September. While it was 17.1pc above August, the rate was also 31.5pc below September 2022.
Meanwhile, in a sign of weakening future demand, permits for the total US housing market in September were at a seasonally adjusted annual rate of 1.473mn. It’s both 4.4pc below August’s rate and 7.2pc lower year-on-year.
Again, this was owed to multi-family construction, with permits of buildings with 5 units or more at a rate of 459,000 for September. This was 14pc lower than August’s rate and 31.6pc lower year on year.
Polymers outlook
PVC demand has been steady to slightly positive in recent months. However, the broader mixed picture in the US housing market has still meant any improvement in PVC demand is limited on a monthly basis and often poor on a yearly comparison. Some PVC buyers and converters are using the last vestiges of good demand in September and October to offload remaining inventories and are running plants at lower rates. Others are trying to closely match their intake of resin to tangible finished goods sales downstream rather than any forward expectations of good demand.
Certain sectors like flooring have benefited from public and private investment into commercial, industrial, and municipal projects spurred by federal investment into infrastructure and manufacturing. However, these gains in the commercial and municipal sectors are not offsetting larger losses in the private residential side of the PVC business, and virtually all PVC end use sectors have been jockeying over limited market share despite the boost in public spending.
Meanwhile, despite housing starts and completions rising in September, demand in upstream material remains muted for the polyurethane products chain. At multiple stops along the polyurethane value chain demand is still classified as weak but steady by market participants.
Much like in PVC, while isocyanate supply is plentiful many market players are holding low inventories keeping a ‘just in time’ supply. Both demand and pricing are not expected to change much through the end of the year.
Polyether polyols, used for polyurethane foams in insulation, have also not seen a pickup in demand. As we exit the height of construction season, polyether polyols are not expected to see much change through 2023.
Expectations for the rest of 2023 and the start of 2024 are turning negative in the PVC and polyurethane markets as high interest rates from the Federal Reserve make building more expensive and price some prospective homebuyers out of the market with higher mortgage rates. Market participants in PVC and the polyurethane chain now hope the back half of 2024 will bring the onset of a more robust recovery in demand.
This is likely tied with broader expectations that interest rates could start to fall back from the multi-decade highs imposed by the Fed, with mid to late 2024 emerging as the earliest possible timeframe rates could fall and US housing construction activity could grow in earnest as a result.
The data and insight used in this article is taken from the Argus Global Polyvinyl Chloride and Argus Polyurethanes services.
Author Aaron May, Catherine Rabe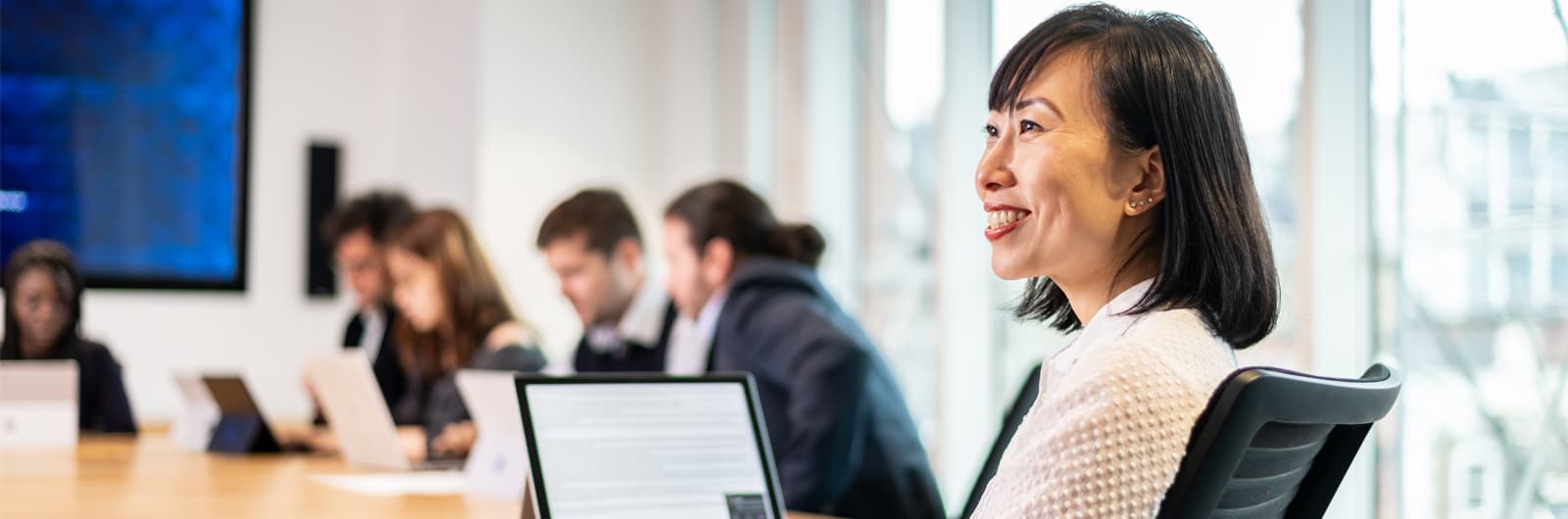