Q&A: Ramaco adding production, sees market growth
Randall Atkins is a founder and chief executive of metallurgical coal producer Ramaco Resources. He also has been involved in energy-related investment and financing activity for over 40 years. In this Q&A, edited for length and clarity, he discusses effects from the Francis Scott Key bridge collapse, his outlook for coal and the company's research projects.
What effect has the Key bridge collapse and Port of Baltimore closing had on Ramaco and the US coal industry in general?
Like most things of that tragic nature, it is going to take longer than everyone expects to actually solve the problem.
I think where it is going to impact producers probably more is on the rails. There will be a need for...producers to rearrange stockpiles and to rearrange where they are going to try and ship, even at reduced levels. Particularly, CSX is going to have an immense logistical complexity to deal with over the near-term.
We do not ship from Baltimore. We have not seen any problems, knock on wood, with our rail shipments post the incident.
What are your long-term projections for metallurgical coal given expectations that low-volatile coal reserves will shrink in coming decades and the steel industry could be in oversupply?
Low vol coal has traditionally been the highest priced coal and the dearest, if you will. High vol A coal has over the last few years grown in importance, and to the extent that there is any new increase in production in the US, it's high vol. What we perceive is that there is going to be a crowding in the high vol space. As a result, our increase in production is primarily in low vol.
As far as the demand side is concerned, we do not believe that blast furnace steel demand is going to decline anytime soon. There's a lot of noise from the green community that hydrogen is going to replace coal in blast furnaces. We took some advice on that from the IEA…and when that question was posed (to IEA), the answer that was given was it would take about $1.5 trillion to build a pilot plant using hydrogen by 2035 and probably about another equal or greater sum to build a commercial facility by 2040. So, I don't lose a lot of sleep on the demand for coal for blast furnaces.
What I do see shifting, however, is the US has held relatively steady at about 20mn short tons (18.1mn metric tonnes) of met coal demand over the last 10 to 15 years. The growth is clearly overseas, and the growth is clearly at the moment in Asia.
When we started back in 2017, and 2018 was really our first year of production, we predominantly sold coal domestically; I think 80pc of our coal went to US steel mills. Now that is almost reversed. We're going to sell probably this year, 70pc overseas, and about a third or less domestically.
With Europe moving towards electric arc furnace technology and significant new blast furnace capacity coming online in Asia, what kind of role will the US play as a coal supplier over the coming years?
It is cheaper to use a blast furnace than electric arc. And the steel that they (Asian companies) mostly require is the heavier steel for cars and buildings and things of that nature. So, they have a bias towards blast furnace capacity.
The US and Europe are very developed economies that are trying to go and wean away from coal, (while) the rest of the world is aggressively moving further into coal. People will shake their heads at the cost that European and American consumers will start to have to pay for that privilege.
We see market growth is still there, but it's a different kind of growth. It will be more in the Asian markets, predominantly some in Europe, some in South America and Africa.
The low vol coal demand in Asia is extremely strong because while they are able to buy high vol product from Australia very inexpensively, they do not have the low vol production. They need that to blend up to get the proper mix in their blast furnaces. There is a very good future for low vol, and that is the direction we are positioning ourselves.
How confident is Ramaco about securing its investments in the longer run given the emphasis on ESG?
What I see is sort of a dichotomy.
In the thermal coal business, there's not a lot of investment in new mining there for the obvious reason that their customer base is declining.
On the met side, it is a bit shortsighted from an investment standpoint because of the composition of the ownership of met coal companies. Virtually every major metallurgical coal producer except for us went through bankruptcy and post-bankruptcy proceedings. Their board composition became essentially distressed debt investors...Their interest was not developing a long-term coal company. Strategically their vision was: "How can we most quickly get money back out of that coal company?"
We are certainly the only coal company that is doubling in size. We produced a little under 4mn st last year. We will be at about 4.5mn st this year. We can maybe go higher, depending upon the market. The market is not strong right now.
The other issue (for coal producers) even when they weren't doing special dividends, is they've now shifted to doing large-scale share buybacks.
You are starting to see the cost curve increase for most domestic coal producers. What you haven't seen, but I think you will probably find over the next probably 18 to 24 months, is you will begin to see depletion kick in. The amount of coal that they are able to produce from their existing operation will begin to decline. And that is strictly a result of not investing in new mine production.
My approach was to kind of be a little bit of an outlier and then approach coal to products as an alternative use, certainly for thermal coal. And that, of course, brought us to rare earth (mineral extraction).
Do you have funding for Ramaco's rare earth materials projects?
Let me step back one step.
We introduced the idea that we actually had rare earth (deposits) in May 2023….When we sent the samples to be tested, they tested them as if they were hard minerals. In other words, they did not combust off the organic material. What we have done since then, is we went back and we had samples that were probably 200-300 parts per million. From a commercial standpoint, we have kind of crossed the Rubicon that this is indeed sufficiently concentrated that it makes commercial sense. Now what we are doing is we are going through a process of further chemical analysis and testing to determine what is the best extraction and refinement technique.
And the last point you raised was financing. We have a very nice growing mining metallurgical business, which can provide the funding to do whatever we want to do on rare earth. I am not too concerned about our financing capability.
Any updates on your coal-to-carbon product projects?
We have looked at a number of different things with the national labs. We started looking at carbon fiber, which could be made from coal and we have got some patents around some very interesting processes.
The areas that we are now focusing on...are using coal to make synthetic graphite. The other thing we are working on is using coal for direct air capture.
We are considering going into a pilot phase sometime starting later this year with Oak Ridge National Laboratory on a synthetic graphite plant. As far as direct air capture, we probably have more work to do. We are also working on that with Oak Ridge. But I would hope that sometime by 2025, certainly 2026, we would perhaps have our first product, quote unquote, to be able to offer into the market. And it would be delightful if it was synthetic graphite.
Related news posts
Overprotectionism harmful for EU stainless: Marcegaglia
Overprotectionism harmful for EU stainless: Marcegaglia
London, 20 September (Argus) — Trade barriers and a focus on protectionist measures alone will not save Europe's increasingly uncompetitive stainless steel industry and have the potential to accelerate deindustrialisation, according to major Italian steelmaker Macegaglia chief executive Antonio Marcegaglia. Speaking on the sidelines of the International Stainless and Special Steel Conference held in Rome this week, Marcegaglia said that an overdose of such measures threatens to reduce long-term demand while incentivising the import of steel-containing finished goods. "While trade measures for correcting unfair international competition are welcomed, this is not beneficial if you think about the whole value chain," he said. "We have seen that despite high duties and safeguards, competition from imports has only increased." Europe's stainless steel sector is under heavy pressure from decreasing demand and growing costs. EU sales of stainless steel producers declined by 26.7pc year on year in 2023 to €16.44bn, with 2024 sales due to decline by a further 18pc to €13.44bn, according to Marcegaglia data. Delegates surveyed by Argus at the conference agreed the industry is severely struggling, with 2024 revenues likely to be below the pre-Covid year of 2019. On the costs side, Marcegaglia said that while Europe already has the challenge of higher energy, labour, transport and capital costs relative to Asia, more recent hikes to key raw material costs have effectively made it uncompetitive on all fronts. The availability of stainless steel scrap is getting tighter in the EU despite the fall in steel production, which together with high ferro-alloy prices has increased volatility for producers. A rising trend of upstream integration among Asian producers has increased their ability to control the costs of their key input, nickel pig iron, causing European scrap to become expensive relative to Asian NPI. Battling an unfavourable cost structure and lower scrap availability, European producers moved to start importing NPI in large volumes this year, despite its environmentally unfriendly nature relative to scrap. Europe's NPI imports from Indonesia equated to 10,000t of nickel metal content in January-July, moving up from zero in 2023, according to Red Door Research managing director Jim Lennon. "The reason for NPI inflows [into Europe] was the differential between the stainless scrap price and NPI," Lennon said at the conference. "NPI was cheaper than stainless steel scrap and so it was a big incentive to bring NPI into the supply chain." Marcegaglia said decarbonisation is a challenge for the European industry given the region is now wholly cost uncompetitive, and suggested the industry agree on green premiums to share CO2 related costs. "Given Europe's already high scrap utilisation, efforts for further improvements are complex and costly," he said. "The steel industry has to balance between environmental and economic sustainability." Delegates at the conference agreed decarbonisation will have to take a back seat as the European industry as a whole focuses on survival. "As far as 2030 net-zero goals are concerned, you can forget about them," industry equipment supplier Alfa Laval Technologies global sourcing manager and supplier development manager Marcus Lindholm said. Marcegaglia said that a possible pathway to recovery for the beleaguered industry is through the pursuit of supply chain co-operation, as current fierce competition between EU players is compounding its profitability problems. The group is strategically looking at further opportunities for upstream integration to stabilise its supply chains and improve its carbon footprint, while enlarging its product range to include both flat and long products. Earlier this week, it announced a £50mn ($66mn) investment to build a new electric arc furnace at its existing plant in Sheffield, in the northeast UK, which will increase the mill's stainless steel products output to over 500,000 t/yr. It is further committed to investment at its Oldbury, UK, tube plant, while also working towards expanding its product range from its Fagersta rolling mill in Sweden. By Raghav Jain Send comments and request more information at feedback@argusmedia.com Copyright © 2024. Argus Media group . All rights reserved.
Malawi Kanyika Nb mine development granted extension
Malawi Kanyika Nb mine development granted extension
London, 20 September (Argus) — Australia-based Globe Metals and Mining has been granted an additional year to begin mining at its Kanyika niobium project in central Malawi. The extension to 27 September 2025 was requested because of delays in finalising a mine development agreement with the government. Kanyika, which will be Africa's first niobium mine, will produce niobium and tantalum oxides for export to western markets, Globe said. The mine will be developed in two phases, with phase 1 scheduled for the start of 2026 and phase 2 for third-quarter 2028. The mine is expected to produce around 3,250 t/yr of niobium and 140 t/yr of tantalum over a 25-year lifespan, which could potentially be extended. Niobium is critical to military, aerospace, space and medical industries, and is becoming increasingly important in quantum electronics, in the manufacture of semiconductors and in the electric vehicle sector, Globe said. By Roxana Lazar Send comments and request more information at feedback@argusmedia.com Copyright © 2024. Argus Media group . All rights reserved.
India's Smiore to boost Mn capacity in Karnataka
India's Smiore to boost Mn capacity in Karnataka
Mumbai, 20 September (Argus) — India's Sandur Manganese and Iron Ore (Smiore) has received approval from the environment ministry to increase its manganese ore capacity in Bellary, Karnataka state. After securing approval from the Karnataka State Pollution Control Board (KSPCB) under the Air and Water Act, Smiore plans to raise its manganese ore production capacity from 430,000 t/yr to 550,000 t/yr. This will pave the way for higher ferro-manganese and silico-manganese production in the near future. But the company did not provide a timeframe for the project. Argus assessed that prices for 60pc grade silico-manganese stood at 66,000-67,000 rupees/t, while prices for 70pc grade ferro-manganese were around Rs69,000-71,000/t ex-works on 19 September. The demand for alloy from domestic steel mills remains limited because of lower buying interest in steel products. The company operates two mines with estimated reserves of about 17mn t of manganese ore and 117mn t of iron ore. Smiore sold about 9,396t of ferro-alloy in the April-June quarter, up by 35pc from a year earlier. By Deepika Singh Send comments and request more information at feedback@argusmedia.com Copyright © 2024. Argus Media group . All rights reserved.
US earmarks $3bn to boost battery supply chain
US earmarks $3bn to boost battery supply chain
Houston, 20 September (Argus) — The US Department of Energy (DOE) has selected 25 projects across 14 states to potentially receive more than $3bn to build out domestic supply of batteries, their components and critical materials including lithium, manganese and graphite. The proposed recipients will "retrofit, expand and build" manufacturing and recycling facilities across the US, targeting different stages of the battery production supply chain, the DOE said on Thursday. Projects include those for advancing direct lithium extraction (DLE) technology, producing cathode active material (CAM) and developing components for battery separators. More than $1bn is planned for five projects, with Standard Lithium and Equinor's SWA Lithium joint venture and TerraVolta Resources each possibly getting $225mn for their DLE undertakings. Cirba Solutions and Group14 Technologies were next with $200mn for the former's lithium-ion battery recycling centre and the latter's silane manufacturing plant, while EnergySys Advanced Systems could receive $199mn for its site, where it intends to produce battery cells. The funding, which will be administered by the Office of Manufacturing and Energy Supply Chains (MESC), is being made available under the Bipartisan Infrastructure Law. Final award totals are contingent on negotiations between applicants and the DOE, along with environmental reviews of each proposed project. The DOE already dispersed more than $1.8bn for 14 projects in October 2022 during the first round of awards funding under the MESC's battery materials processing and battery manufacturing and recycling programmes. By Alex Nicoll List of selected projects Company name Project location Proposed funding amount Targeted output Proposed production capacity SWA Lithium LLC Lewisville, AR $225,000,000 Lithium carbonate 45,000t TerraVolta Resources Texarkana region $225,000,000 Lithium carbonate 25,000t Cirba Solutions Columbia, SC $200,000,000 Metal salts from recycled batteries 60,000t of batteries Group14 Technologies Moses Lake, WA $200,000,000 Silane gas N/A EnerSys Advanced Systems Piedmont, SC $198,679,760 Lithium-ion battery cells 5 GW/h South32 Hermosa Patagonia, AZ $166,175,802 Manganese sulfate monohydrate 185,000t Element 25 (Louisiana) Baton Rouge, LA $166,128,094 Manganese sulfate monohydrate 65,000t SKI US Orangeburg, SC $150,000,000 Synthetic graphite 25,000t Form Energy Weirton, WV $150,000,000 Iron-air batteries 20GWh Clarios Circular Solutions Florence, SC $150,000,000 CAM from recycled batteries 20,000t American Battery Technology South Carolina $150,000,000 Battery materials from recycled batteries 100,000t Revex Technologies Champion MI; Gwinn, MI $145,000,000 Nickel concentrate black mass from spent batteries 21,250t 16,000t Honeywell International Geismar, LA $126,586,497 Lithium bis(fluorosulfonyl)imide N/A Ascend Elements Hopkinsville, KY $125,000,000 Recycled graphite N/A Urbix Muscle Shoals, AL $124,638,300 Coated spherical purified graphite 10,000t DOW Chemical US Gulf Coast $100,000,000 Carbonate solvents N/A Forge Battery Morrisville, NC $100,000,000 Lithium-ion battery cells 3GWh Mitra Future Technologies Muskegon, MI $100,000,000 Lithium-iron-phosphate (LFP) CAM 30,000t Albemarle US Charlotte, NC $67,075,044 Lithium metal anode material 50t NanoGraf Flint, MI $60,000,000 Silicon monoxide anode material 2,500t Li Industries Kettering, OH $55,243,798 LFP CAM 10,000t Blue Whale Materials Bartlesville, OK $55,232,669 Black mass from recycled batteries 50,000t Braskem America La Porte, TX $50,000,000 Ultra-high molecularweight polethylene N/A Cabot Van Buren Township, MI $50,000,000 Carbon nanotubes Conductive additive dispersions 1,000t 12,000t Solid Power Operating Thornton, Co $50,000,000 Sulfide-based solid electrolyte N/A — US Department of Energy Send comments and request more information at feedback@argusmedia.com Copyright © 2024. Argus Media group . All rights reserved.
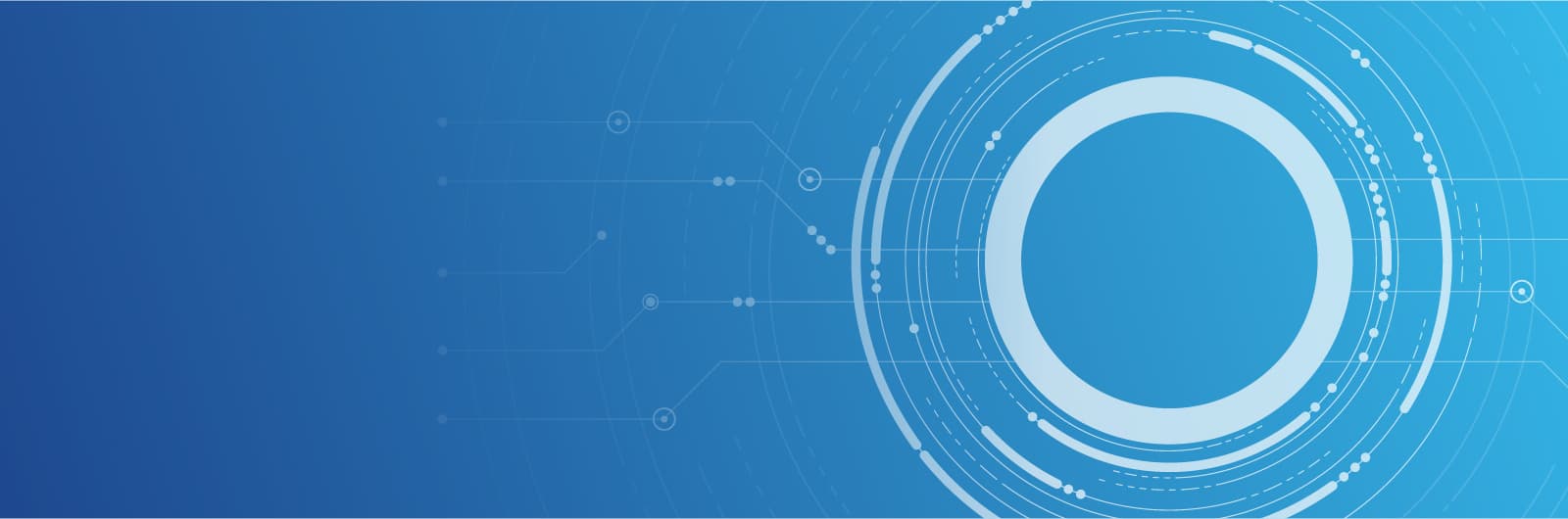
Business intelligence reports
Get concise, trustworthy and unbiased analysis of the latest trends and developments in oil and energy markets. These reports are specially created for decision makers who don’t have time to track markets day-by-day, minute-by-minute.
Learn more