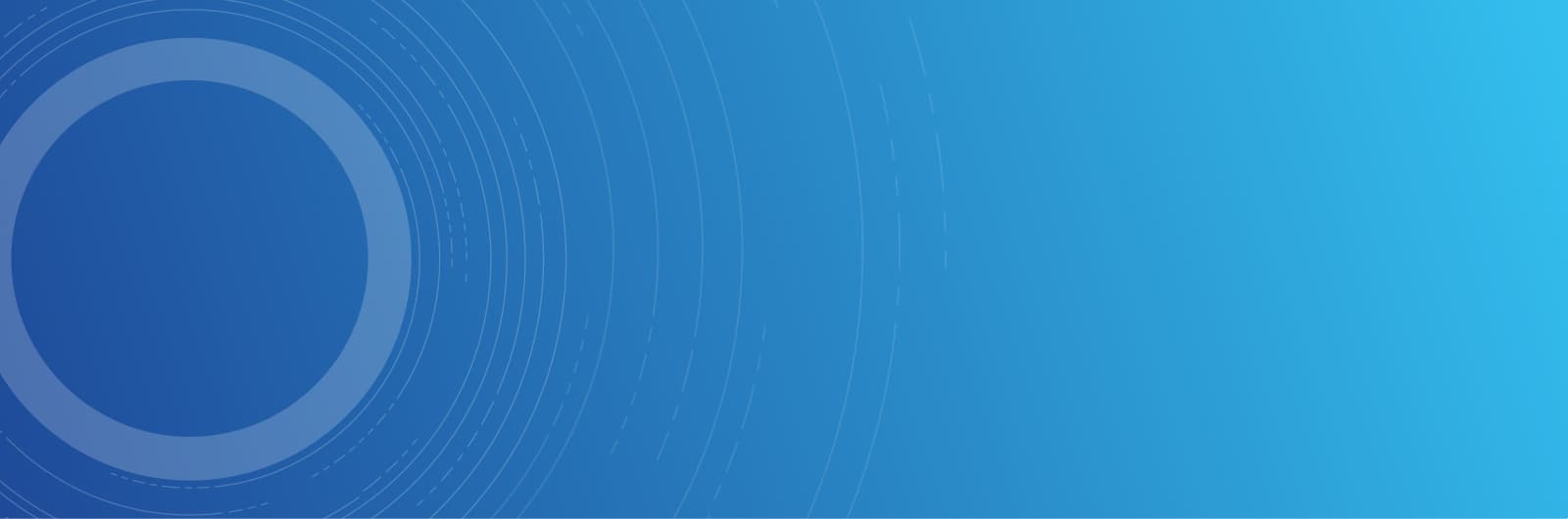
Steam cracker capacity addition: relief in sight
Global steam cracker operating rates have been trending downward from 89pc in 2018 to 79pc in 2023, driven by the combination of high-capacity increase and slower economic growth in recent years.
In Argus's latest Ethylene Analytics, a recovery is forecast to take place in the coming years as the recent wave of new capacity cools off, absorbing demand growth before the second wave of capacity addition outgrows demand from 2027-2029. This recovery is based on a modelled assumption of modest growth in the global economy and a slowdown in capacity expansion. Historically, olefins demand growth has trended in line with GDP growth on a global basis; in recent years this relationship has disconnected. This was a result of the imbalance between the service and manufacturing industries, but we anticipate the trend will revert sooner or later moving forward.
The petrochemical industry is experiencing high levels of upcoming capacity over the next five years. On a global level, ethylene and propylene capacity is expected to increase by 47.4mn t (4pc) and 44.0mn t (5pc), respectively, over the next five years while global capacity growth from 2018 to 2023 averaged at 4.5pc/yr for both ethylene and propylene. Most investment in ethylene production has gone into steam crackers where ethylene is the main product and propylene is produced as a co-product. Propylene will see a high-capacity increase from not only steam crackers but also from propane dehydrogenation (PDH) projects, which will delay the recovery of global propylene operating rates.
The first wave of ethylene capacity addition is cooling off, but a second wave is expected to kick off in 2026. However, propylene is currently undergoing its wave of capacity addition before seeing a slowdown from 2028 onward. On the propylene side of the olefins chain, 50pc of the upcoming capacity will come from PDH, 34pc from steam crackers and the rest will be a combination of sources from refinery, coal, and methanol.
Operating rates in all regions are being negatively impacted by the combination of high-capacity increase and slower global economic growth. Olefins demand has experienced slower growth over the past two years, with negative growth in 2022 as a result of high inflation and lower consumer spending.
Based on current market fundamentals there have been project delays across most regions and also rationalisation from uncompetitive units. With steam crackers running at lower-than-normal operating rates, rationalization of capacities is a significant unknown as what assets are to shut down are dependent on many factors such as company financials, politics, and integration factors. This makes the rationalization of specific units tough to predict.
As western nations are experiencing slower GDP growth, developing nations will be the key regions for olefins growth. We are seeing a slowdown in Chinese and northeast Asian GDP, but south Asian GDP has been holding strong. Polymer demand, which accounts for more than half of olefins consumption will be the main driver of olefins demand (65pc of ethylene gets consumed into PE and 71pc of propylene gets consumed into PP globally). From a supply perspective, 17pc (8mn t) of all upcoming cracker projects have yet to start construction, which will give operating rates a boost if delayed. Given the slowdown in global economic growth in the past two years, high interest rates, and inflation, the overall outlook is fairly bearish. Consumer spending, household disposable income, economic growth, project timelines, and rationalization from uncompetitive production facilities will be the main indicators of how quickly it will take for operating rates to recover.
Current announced projects
In the past five years, most steam cracker capacity increases took place in China and the trend is expected to persist over the next five years based on announced projects, but most regions are investing. Other Asian countries such as India, South Korea, Vietnam, and Indonesia are also investing. A total of 25.6mn t and 32.9mn t of ethylene and propylene capacity is expected to come online in China over the next five years. Below is the summary of upcoming stream cracker projects globally.
Chinese projects that are currently under construction include Wanhua Chemial, Yulongdao Refining & Petrochemical, Sinopec, Jilin Petrochemical and more. Joint venture steam cracker projects in China between domestic producers and multinational corporations have also started construction which includes Sabic-Fujian Petrochemical, Ineos Sinopec Tianjin, Shell CNOOC Petrochemical, BASF Zhanjiang, and ExxonMobil. These projects will increase ethylene capacity by 21.8mn t over the upcoming five years. Asian nations excluding China includes S-oil South Korea, Hindustan Petroleum India, Lotte Chemical Indonesia have also started construction which totals 5.2mn t of ethylene capacity.
Borouge, SATORP and a joint venture between CP Chem and Qatar Energy in the Middle East are also investing in new crackers with a total capacity addition of 5.2mn t. In Europe, Ineos Project One and PKN Orlen have announced projects while Sabic UK invested in a green project. The Sabic project involves restarting and converting its current cracker to run on hydrogen.
Russia has steam cracker projects slated to start up in the five-year span, including Nizhnekamskneftekhim, Irkutsk Oil, Baltic Chemical, and Amur GCC while Uzbekistan has also announced an expansion from Gas Chemical Complex. North America has three projects slated to come on over the next five years that will increase its capacity by 3.6mn t. North American projects include Shintech US, Joint venture CP Chem Qatar Energy, and Dow in Canada.
Argus’s Ethylene Analytics includes a global plant-level capacity dataset detailing expected project timelines.
Author: Dhanish Kalayarasu
Date: 15/05/2024
Spotlight content
Related news
Brazil turpentine shipments delayed by port backlogs
Brazil turpentine shipments delayed by port backlogs
London, 25 July (Argus) — Brazilian gum turpentine export shipments are being delayed by isotank availability that is significantly tightening owing to difficult booking schedules and port congestion in Asia-Pacific. Delays are close to a month for shipments going to India, sources said. In some cases vessels have been at a port for weeks, adding to delays caused by difficult booking schedules. With a number of Brazilian ports handling more goods than before, including Brazil's key port for pine chemicals exports Santos where cargo in the first half of 2024 hit a record for the period. There has also been congestion at Asian ports. "There is chaos in southeast Asia," a buyer in Asia said. "Ship lines confirm bookings just to cancel them later." India is Brazil's largest gum turpentine buyer, with most going into the camphor and aroma chemical markets during peak season in the second half of the year. India imported 12,509t of gum turpentine from Brazil in 2023, Global Trade Tracker (GTT) data show, the second highest since at least 2015. In 2022, India imported a record 12,944t of Brazilian gum turpentine, according to GTT. Volatile gum turpentine freight rates from Brazil to India has now incentivised several Brazilian suppliers to shift from cif to fob-based sales to avoid the risk of unpredictable isotank costs. Gum turpentine freight rates from Brazil to India have risen to around $7,000-7,500 per isotank from $2,500-3,000 levels in January 2024, one customer said. The escalating freight rates continue to put upwards pressure on the Brazil gum turpentine market, with prices rising amid steady demand from India, the US and Mexico. Brazilian Pinus elliottii gum turpentine spot export prices were assessed at $2,200-$2,250/t fob, Brazil port, on 15 July, up by more than 25pc from $1,650-$1,800/t fob, Brazil port, at the same time last year. The export prices are higher this year because of stronger demand from the US flavours and fragrance market, firm business activity into India and Mexico and lower buyer stocks. By Leonardo Siqueira Send comments and request more information at feedback@argusmedia.com Copyright © 2024. Argus Media group . All rights reserved.
Feedstock imports shake up US biofuel production
Feedstock imports shake up US biofuel production
New York, 24 July (Argus) — Waste from around the world is increasingly being diverted to the US for biofuel production, helping decarbonize hard-to-electrify sectors like trucking and aviation. But as refiners turn away from conventional crop-based feedstocks, farm groups fear missing out on the biofuels boom. Driven by low-carbon fuel standards (LCFS) in states like California, US renewable diesel production capacity has more than doubled over the last two years to hit a record high of 4.1bn USG/yr in April according to the Energy Information Administration. Soybean and canola processors have invested in expanding crush capacity, expecting future biofuels growth to lift vegetable oil demand. But policymakers' growing focus on carbon intensity, a departure from the long-running federal renewable fuel standard (RFS) that sets volume mandates for broad types of fuel, primarily benefits waste feedstocks, which generate larger LCFS credits because they are assessed as producing fewer emissions. Argonne National Laboratory's GREET emissions model, which has been modified by federal and California regulators for clean fuels programs, factors in emissions sources like fertilizers and diesel use on farms for virgin vegetable oils but not for used oils sourced from cooking operations. Refiners trying to maximize government subsidies are thus sourcing waste-based feedstocks from wherever they can find them. Through May this year, imports to the US under the tariff code that includes used cooking oil (UCO) and yellow grease rose 90pc from year-prior levels to more than 1.8bn lb (844,000t). While China represents most of that, sources are diverse, with significant sums coming from Canada, the UK, and Indonesia. Imports of inedible and technical tallow, waste beef fat that can be turned into biofuels, have also risen 50pc so far this year to 800,000lb on ample supply from Brazil. While soybean oil was responsible for nearly half of biomass-based diesel production in 2021, that share has declined to around a third over the first four months this year as imports surge (see graph). "Every pound of imported feedstock that comes in displaces one pound of domestically sourced soybean oil or five pounds of soybeans," said Kailee Tkacz Buller, chief executive of the National Oilseed Processors Association. Even as LCFS and RFS credit prices have fallen over the last year, hurting biofuel production margins and threatening capacity additions , imports have not slowed. Feedstock suppliers, many from countries with less mature biofuel incentives and limited biorefining capacity, might have few options domestically. And exporting to the US means they can avoid the EU's more prescriptive feedstock limits and mounting scrutiny of biofuel imports. More ambitious targets in future years, particularly for sustainable aviation fuel, "will create a lot of competition for UCO in the global market," said Jane O'Malley, a researcher at the International Council on Clean Transportation. But for now, "the US has created the most lucrative market for waste-based biofuel pathways." Incentives for US refiners to use waste-based feedstocks will only become stronger next year when expiring tax credits are replaced by the Inflation Reduction Act's 45Z credit, structured as a sliding scale so that fuels generate more of a subsidy as they produce fewer greenhouse gas emissions. While essentially all fuel will receive less of a benefit than in past years since the maximum credit is reserved for carbon-neutral fuels, the drop in benefits will be most pronounced for fuels from vegetable oils. Granted, President Joe Biden's administration wants the 45Z credit to account for the benefits of "climate-smart" agriculture, potentially helping close some of the assessed emissions gap between crop and waste feedstocks. But the administration's timeline for issuing guidance is unclear, leaving the market with little clarity about which practices farmers should start deploying and documenting. "While a tax credit can be retroactive, you can't retroactively farm," said Alexa Combelic, director of government affairs at the American Soybean Association. Squeaky wheel gets the soybean oil The concerns of agricultural groups have not gone unnoticed in Washington, DC, where lawmakers from both parties have recently called for higher biofuel blending obligations, prompt 45Z guidance, and more transparency around how federal agencies scrutinize UCO imports. There are also lobbying opportunities in California, where regulators are weighing LCFS updates ahead of a planned hearing in November. At minimum, agricultural groups are likely to continue pushing for more visibility into the UCO supply chain, which could take the form of upping already-burdensome recordkeeping requirements for clean fuels incentives and setting a larger role for auditors. Fraud would be hard to prove, but two external groups told Argus that the Biden administration has indicated that it is looking into UCO collection rates in some countries, which could at least point to potential discrepancies with expected supply. More muscular interventions, including trade disincentives, are also possible. Multiple farm associations, including corn interests frustrated that the country's first alcohol-to-jet facility is using Brazilian sugarcane ethanol , have asked the Biden administration to prevent fuels derived from foreign feedstocks from qualifying for 45Z. The possible return of former president Donald Trump to the White House next year would likely mean sharply higher tariffs on China too, potentially stemming the flow of feedstocks from that country — if not from the many others shipping waste-based feedstocks to the US. Protectionism has obvious risks, since leaving refiners with fewer feedstock options could jeopardize planned biofuel capacity additions that ultimately benefit farmers. But at least some US agriculture companies, insistent that they can sustainably increase feedstock production if incentives allow, see major changes to current policy as necessary. By Cole Martin Waste imports crowd out soybean oil Send comments and request more information at feedback@argusmedia.com Copyright © 2024. Argus Media group . All rights reserved.
US House passes waterways bill
US House passes waterways bill
Houston, 23 July (Argus) — The US House of Representatives overwhelmingly approved a bill on Monday authorizing the US Army Corps of Engineers (Corps) to tackle a dozen port, inland waterway and other water infrastructure projects. The Republican-led House voted 359-13 to pass the Waterways Resources Development Act (WRDA), which authorizes the Corps to proceed with plans to upgrade the Seagirt Loop Channel near Baltimore Harbor in Maryland. The bill also will enable the Corps to move forward with 160 feasibility studies, including a $314mn resiliency study of the Gulf Intracoastal Waterway, which connects ports along the Gulf of Mexico from St Marks, Florida, to Brownsville, Texas. Water project authorization bills typically are passed every two years and generally garner strong bipartisan support because they affect numerous congressional districts. The Senate Environment and Public Works Committee unanimously passed its own version of the bill on 22 May. That bill does not include an adjustment to the cost-sharing structure for lock and dam construction and other rehabilitation projects. The Senate's version is expected to reach the floor before 2 August, before lawmakers break for their August recess. The Senate is not scheduled to reconvene until 9 September. If the Senate does not pass an identical version of the bill, lawmakers will have to meet in a conference committee to work out the differences. WRDA is "our legislative commitment to investing in and protecting our communities from flooding and droughts, restoring our environment and ecosystems and keeping our nation's competitiveness by supporting out ports and harbors", representative Grace Napolitano (D-California) said. By Meghan Yoyotte Send comments and request more information at feedback@argusmedia.com Copyright © 2024. Argus Media group . All rights reserved.
Japan’s Resonac to optimize petchem business
Japan’s Resonac to optimize petchem business
Tokyo, 23 July (Argus) — Japanese petrochemical producer Resonac plans to optimize part of its petrochemical business by creating a new wholly-owned subsidiary by 1 August. Resonac decided on 23 July to set up Crasus Chemical, which will take over production of basic petrochemical goods from Resonac. It aims to set up the subsidiary as an independent, listed company to clarify and facilitate performance evaluations and to simplify a chain of command to speed up decision making. Resonac plans to achieve quicker decarbonization of its petrochemical production and to enhance competitiveness and profit growth. Crasus will be in charge of manufacturing and selling basic petrochemical goods like ethylene and propylene, goods made from acetic acid and synthetic resins. Resonac owns the 618,000 t/yr Oita ethylene cracker in south Japan's Oita prefecture that will will also be transferred to Crasus. Petrochemicals has accounted for around 20pc of Resonac's sales revenues. Japan's petrochemical firms have attempted to optimize their businesses with intensifying international competition and shrinking domestic demand. Mitsubishi Chemical has also tried to reorganize its basic petrochemical business, although it has yet to announce firm plans. By Nanami Oki Send comments and request more information at feedback@argusmedia.com Copyright © 2024. Argus Media group . All rights reserved.
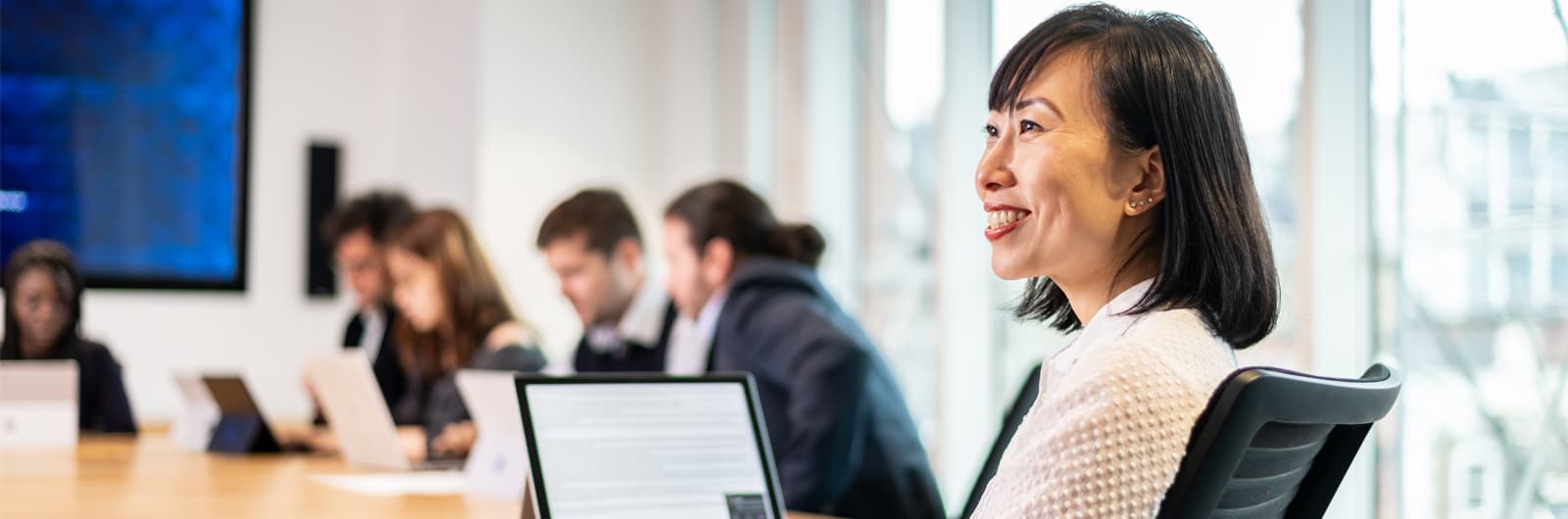